In the ever-evolving world of management and continuous improvement, the PDCA ou Plan do Control Act stands out as a critical framework for organizations striving for excellence. This iterative process, which encompasses four essential stages—Plan, Do, Check, and Act—provides a structured approach to problem-solving and process enhancement. Understanding how to effectively implement this methodology can lead to significant improvements in productivity, efficiency, and overall performance.
The PDCA cycle, often referred to as the Deming Cycle, is not just a tool for quality control; it is a philosophy that encourages organizations to embrace change and innovation. By systematically planning and executing strategies, checking results, and acting on findings, businesses can adapt to market demands and continuously evolve. This article delves into the intricacies of the PDCA ou Plan do Control Act, exploring its benefits, implementation strategies, and real-world applications.
Whether you are a small business owner, a project manager, or part of a large corporation, understanding the PDCA cycle can empower you to drive meaningful change within your organization. Join us as we explore the various facets of this powerful management tool and discover how it can be leveraged to achieve sustainable success.
What is PDCA ou Plan do Control Act?
The PDCA ou Plan do Control Act is a four-step management method used for the control and continuous improvement of processes and products. It was popularized by W. Edwards Deming, a renowned statistician and quality management expert. The cycle includes:
- Plan: Identify an opportunity and plan for change.
- Do: Implement the change on a small scale.
- Check: Use data to analyze the results of the change and determine whether it met expectations.
- Act: If the change was successful, implement it on a wider scale, and continuously assess the process.
How Does PDCA ou Plan do Control Act Enhance Quality Management?
Quality management is essential for any organization aiming to remain competitive. The PDCA cycle enhances quality management by fostering a culture of continuous improvement. Instead of relying on a single, rigid plan, organizations can adapt their strategies based on real-time data and feedback.
What Are the Key Benefits of Implementing PDCA?
Implementing the PDCA ou Plan do Control Act offers numerous advantages:
- Increased Efficiency: Streamlines processes and eliminates waste.
- Enhanced Communication: Encourages collaboration among teams.
- Data-Driven Decisions: Empowers management to make informed choices based on empirical evidence.
- Fosters Innovation: Promotes a culture of experimentation and learning.
How Can Organizations Effectively Implement PDCA?
Successful implementation of the PDCA ou Plan do Control Act requires a strategic approach. Here are key steps organizations can follow:
- Engage Stakeholders: Involve all team members in the planning process to ensure buy-in and diverse perspectives.
- Set Clear Objectives: Define specific, measurable goals that align with the organization's mission.
- Monitor Progress: Use key performance indicators (KPIs) to track the effectiveness of changes.
- Revise and Adapt: Be prepared to iterate the process based on feedback and results.
What Role Does Leadership Play in PDCA Implementation?
Leadership is vital to the success of the PDCA ou Plan do Control Act. Effective leaders foster an environment of trust and open communication, encouraging team members to share ideas and feedback throughout the cycle. By modeling a commitment to continuous improvement, leaders inspire their teams to embrace the PDCA methodology wholeheartedly.
How is PDCA Applied in Different Industries?
The versatility of the PDCA cycle allows it to be applied across various industries. Here are a few examples:
- Manufacturing: Used for quality control processes and production efficiency.
- Healthcare: Implementing PDCA for patient safety and service improvement.
- Education: Enhancing curriculum development and administrative processes.
- IT Services: Streamlining software development and project management.
What Challenges Are Associated with PDCA Implementation?
While the PDCA ou Plan do Control Act offers numerous benefits, organizations may encounter challenges:
- Resistance to Change: Employees may be hesitant to adopt new processes.
- Lack of Training: Insufficient understanding of the PDCA cycle can lead to ineffective implementation.
- Resource Constraints: Limited time and budget may hinder the execution of the cycle.
How Can Continuous Improvement Be Sustained with PDCA?
Sustaining continuous improvement through the PDCA ou Plan do Control Act involves embedding the cycle into the organizational culture. Organizations should:
- Regularly Review Processes: Schedule routine assessments of workflows and outcomes.
- Encourage Innovation: Create a safe space for employees to suggest improvements.
- Celebrate Successes: Recognize and reward achievements to motivate ongoing participation.
Conclusion: Embrace the PDCA Cycle for Lasting Change
The PDCA ou Plan do Control Act is more than just a management tool; it is a mindset that encourages organizations to strive for excellence. By embracing the cycle, businesses can foster a culture of continuous improvement, leading to enhanced efficiency, innovation, and success. As you embark on your journey with the PDCA cycle, remember that the key to lasting change lies in your commitment to the process and your willingness to adapt and grow.
Embracing The Bold: Make It Trashy Torchy's
Exploring The Life And Legacy Of Норман Спенсер Чаплин
Exploring The Expression: Como Haz Estado O Como Has Estado


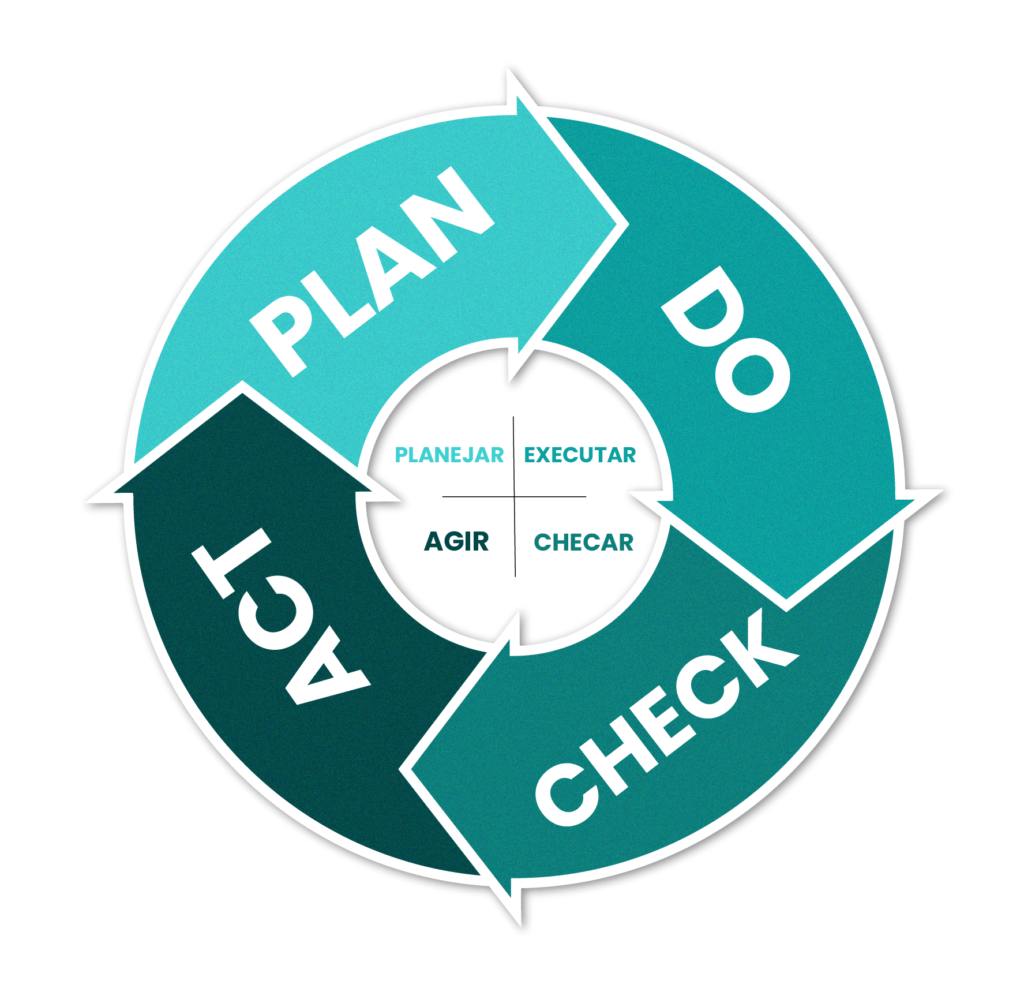